Our medical tubing capabilities
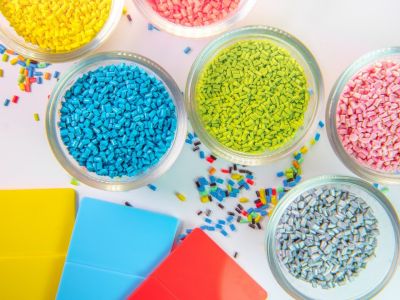
Everyday materials
We use standard grade materials including polyether block amide (PEBA), PET, polyurethane, polycarbonate and thermoplastic elastomer materials.
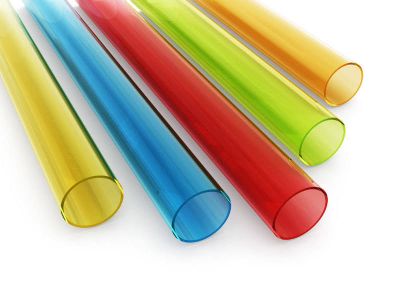
Common processes
Our process and regulatory expertise, strong supplier relationships and equipment availability keep lead times short and help ensure the success of your medical tubing.
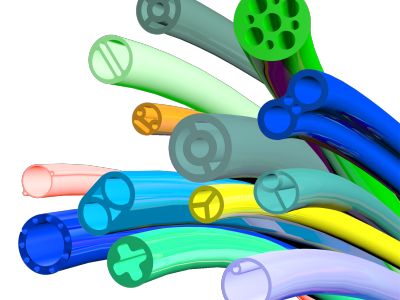
Custom applications
Our technical and processing expertise enables us to extrude a wide range of materials, offering a custom extrusion solution specific to your requirements.
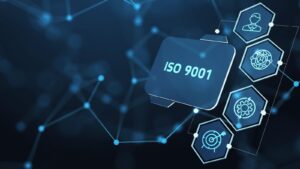
Quality manufacturing standards
Our manufacturing facility meets the standards of ISO 13485 and 9001, reaffirming our goal of maintaining a quality system of the highest possible standard.
Why Choose Us
Our experts design the catheter component solutions you need
You can count on our experienced engineers to develop, design, and implement extrusion needs to deliver custom extrusions while maintaining unparalleled quality.
We will work with you to conceptualize a detailed design, assisting through engineering designs, materials selection, and manufacturing.
Our material experts partner with the world’s best material manufacturers to bring you the latest innovations in polymer technology and performance.